The Facts You Need To Know About Composite Manufacturing
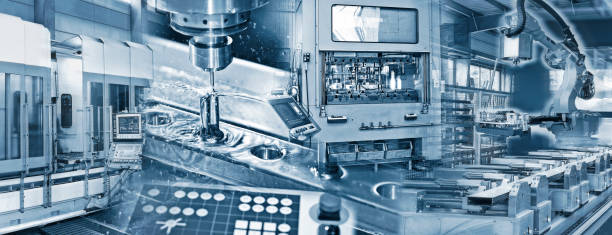
The demand for light affordable, robust, and yet, flexible solutions for many
branches of the economy make composite materials a logical and easy choice for
countless industries of the composite parts manufacturing industry. They are on
the rise when it comes to creating the basic components of aircraft and
automotive structures, for instance, uniting the best qualities you can find in
different traditional materials. Let's look at the advantages and features of
these materials that can help us understand why they're so popular and
preferred.
First, a Definition
The term "composites" can be defined as a mix of elements derived from
natural or artificial sources. The elements should have distinct chemical and
physical properties, which would be able to complement and enhance one another
and enhance the unique properties of the final product. Whenever you require a
useful content on carbon fiber parts manufacturing, look at this website.
The qualities of the raw material are not altered or lost, they are enhanced
due to the mixture. The goal of combining elements with different individual
attributes is to make the finished product stronger, more efficient and durable
than its parts.
What is the basis of composites?
Composites are made from a polymer-based matrix that is reinforced and
fortified by an either artificial or natural reinforcement fiber element. It's
the matrix that serves as a protection against environmental damages as well as
load distribution. The matrix is reinforced by fibers which reduces the
possibility of breaking or cracks.
The composite parts manufacturing process is rather lengthy and complicated,
but if you are seeking to know details about the various steps involved it is a
fantastic guide with lots of details. It is usually only two primary components.
It is possible to add any kind of filler or enhancement based on the industry,
but most composite products are made up of a mix of resin and fiber.
The advantages of composite materials
Composite materials have the biggest advantage of being lightweight and
stiff. They're around two-thirds lighter than an aluminum component of the same
size, while offering the same sturdiness and stability. We have a fantastic
source for engineering due to the ease of the material's moldability and
bendability.
The flexibility of the matrix can be used to create complex shapes without
the use of special tools can be explained by the fact that the geometry of the
object is created by the process of making it solid. It's also very robust, and
is able to be withstand radiation, heat, and dampness and various other outside
influences without suffering damage or losing its properties.
A few words on the negatives
Because they are extremely difficult to break, these materials can make it
very difficult to tell the extent to which an interior structure has suffered
any harm. This is probably the greatest issue engineers have to face when using
composite
materials outer layers for their structures. The aluminum layer will rip
easily and leave enough details about the overall condition of the structure.
This is one of the major issues when dealing with these types of mixtures.
Composite surfaces can be difficult to repair and therefore are more
costly.
The material used in composite manufacturing tends to be more sensitive to
temperatures than the other conventional materials. It begins to weaken about
150°, which means the possibility of a fire can have damaging consequences for a
part made of composite. Apart from the fact that the process of burning can lead
to the risk of inhaling harmful substances released by the resin, higher
temperatures could cause the structure to suffer irreparable damage.
Composite Manufacturing: Challenges
The fact that traditional materials like aluminum and plastic are less
expensive than composites is a huge. Add to this the problem of being unable to
automatize all manufacturing processes. This means we often have to create
costly products manually. Also, there is the issue of standardization, designed
to be used with traditional materials in some industries, like shipbuilding, for
instance. The standards are so stringent and specific that composites fail to
meet the requirements for a variety of reasons. Newer software programs can
successfully implement automation in composite parts manufacturing. This will
increase the chance of starting mass production across all areas of the
business.
Uses
Composites are utilized by residential and commercial construction companies
to replace the wooden frames we all know. The addition of plastic to the mix
ensures that the frame is not susceptible to rot, damp and termites, thus
extending the life of the structure. Any outdoor elements which are subject to
harsh weather conditions benefit from a composite construction. Just imagine not
having to repair your roof for years to come or maintain it in any other way,
either.
The lightweight of composites makes it an ideal material for use in the
aviation and automotive industries. This enables significant fuel savings
without compromising stability on the ground or on the air. When human lives and
safety are at risk, durability is essential. Today, water vessels are often made
of decaying wood or heavy metal that is bound to become rusty. Thermoplastics
and fiberglass make sure that the vessel stays in the water and doesn't suffer
cracks, or other forms of corrosion or damage, despite frequent contact with
salt water and air.
Composites are incredible when it comes to making bulletproof jackets and other ballistic protection devices or products. Certain body armors protect against flames as well as certain explosives as well and can help save hundreds of lives and also preventing severe injuries.
Comments
Post a Comment